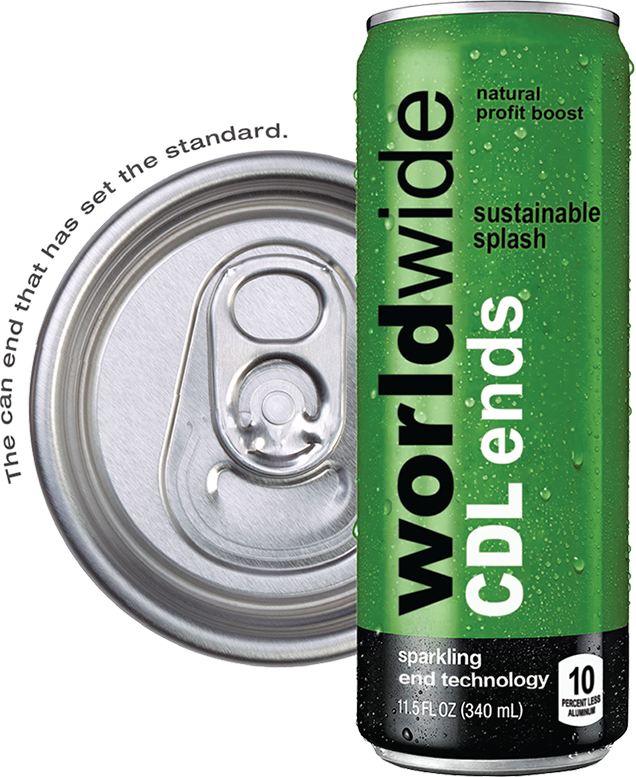
Since 2005, the CDL beverage end has helped brand owners and can makers achieve sustainability and cost savings goals through reduced aluminum consumption.
CDL is recognized as the industry benchmark for aluminum beverage ends.
Container Development LTD (CDL)
CDL was formed in 1997 to develop a new generation of strong, lightweight beverage ends. Today, with an annual production rate of over 200 billion ends and growing, CDL is the undisputed leader in the global market. CDL is the holding company that licenses this technology.
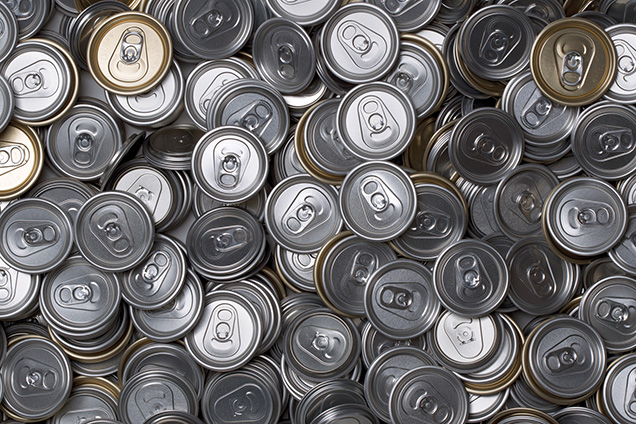
The end that set the standard
- Over 10% less aluminum vs. B64
- No reductions in end performance
- Same filling speed & standard double seaming technology
- Robust performance allows new innovations and materials
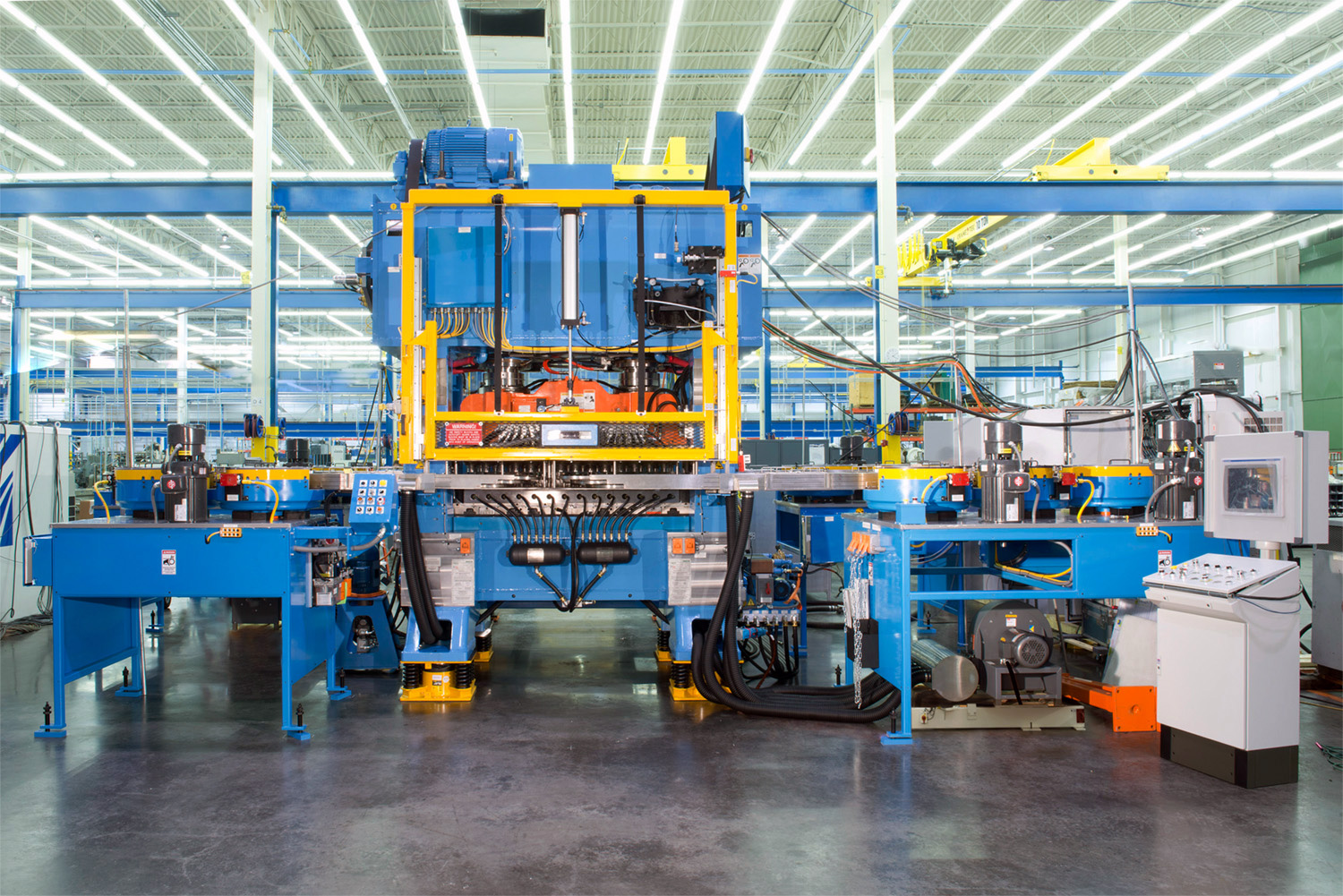
Container Manufacturing LTD (CML)
CML is not a can maker, but a separate, affiliated company established to supply equipment, tooling, installation support and training necessary for the vital transfer of CDL technology to CDL licensees.
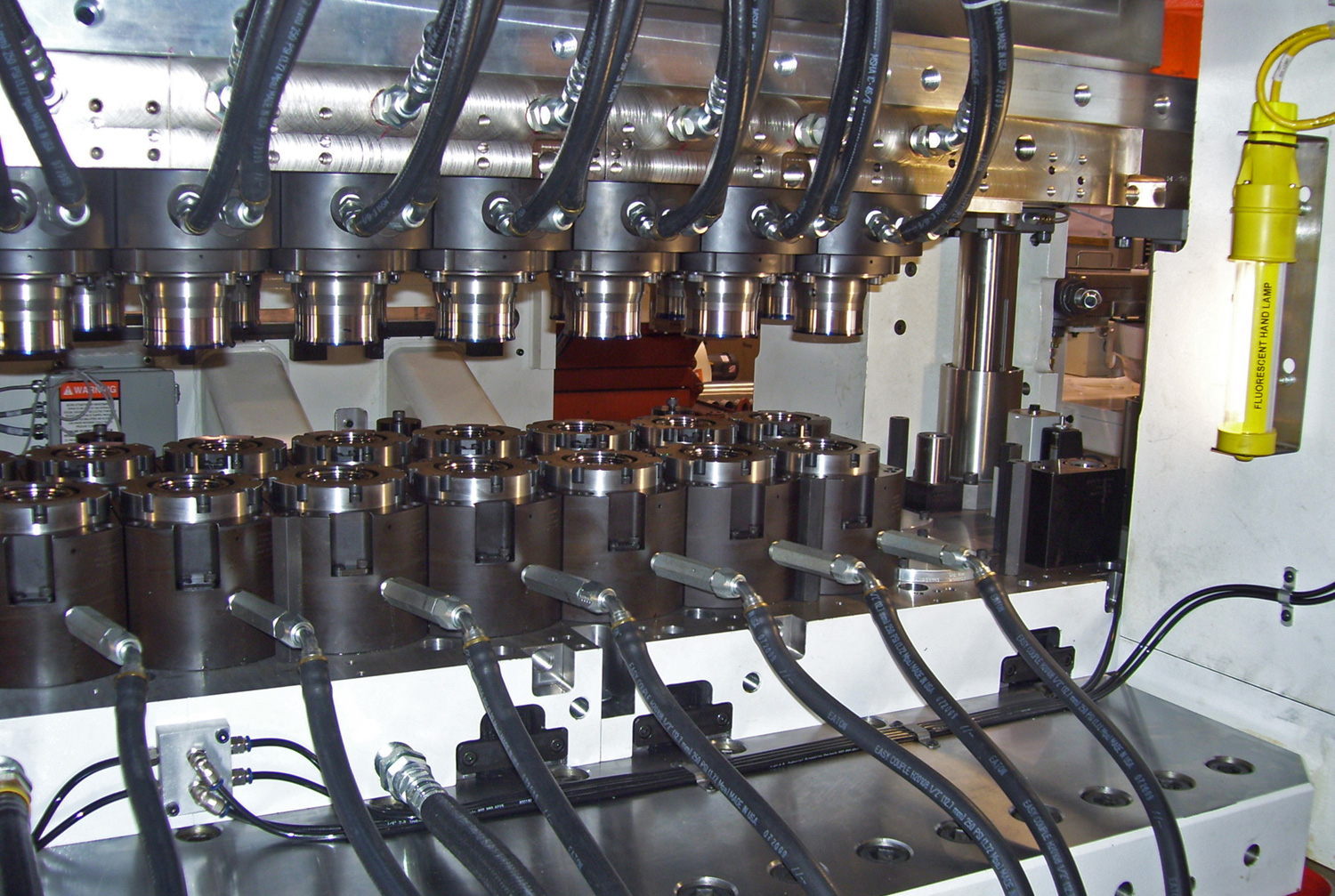
Systems that are right for you
- CML provides wide and narrow shell systems
- New shell systems or retool existing
- Over 130 CDL systems worldwide today
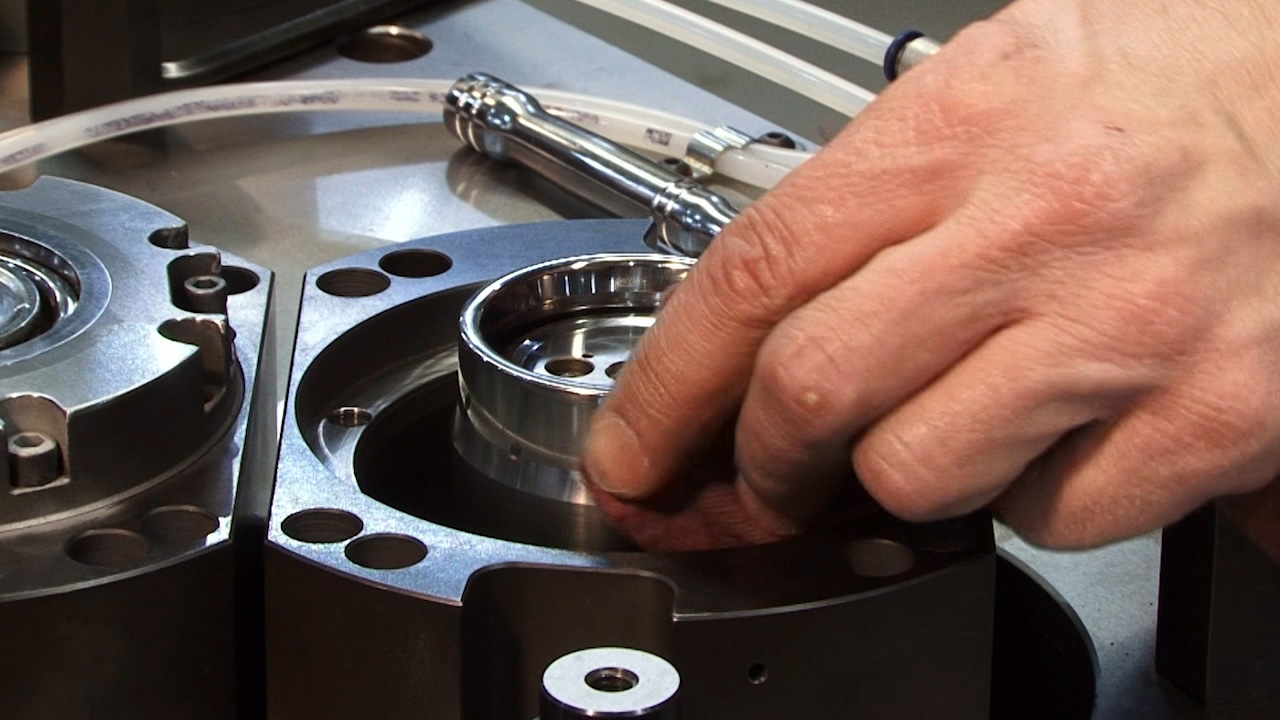
Continued, on-going support
- OEM replacement parts for reliable quality
- Training to help you get the most productivity
- Field service
- Expertise and support for the life of your system